In any aspect of life, whether it be in a professional setting or our endeavors, mistakes are bound to happen. However, when it comes to specific industries or tasks, even the most minor errors can have significant consequences. That is why mistake proofing, also known as poka-yoke, has become an essential practice to prevent errors and ensure quality. By implementing effective strategies and techniques, organizations can minimize the likelihood of mistakes occurring, resulting in improved productivity, customer satisfaction, and overall success. In this comprehensive guide, we will delve into the world of mistake proofing, exploring its benefits, fundamental principles, and practical methods that you can utilize to create a culture of excellence and error-free operations. This guide will equip you with the knowledge and tools needed to prevent errors and achieve optimal results.
Table of Contents
- Mistake proofing
- When to Use Mistake Proofing
- Benefits of Mistake Proofing
- Principles of Mistake Proofing
- Setting and regulatory functions
- Mistake Proofing procedure
- Example
- Conclusion
Introduction
Mistake-proofing, also known as Poka-Yoke, has its roots in Japan, where Shigeo Shingo introduced it in the 1960s. Initially called “Baka-Yoke” (fool-proofing), it was later refined to “Poka-Yoke.“ This concept became a fundamental element of the Toyota Production System (TPS), emphasizing error prevention and detection. It has since transcended the automotive industry and is now used globally in Lean and Six Sigma methodologies to eliminate defects and enhance efficiency in various sectors. Mistake proofing involves designing systems and processes to make errors nearly impossible or readily detectable. Its history highlights its ongoing relevance for quality improvement and waste reduction.
1. Mistake Proofing
Mistake proofing is a technique that involves using automatic devices or methods to either render errors impossible or immediately highlight them once they occur. This approach is commonly employed for process analysis.
It’s main goal is to prevent and quickly detect defects, reducing the chance of errors and improving workflow efficiency. When total prevention or detection isn’t possible, it aims to minimize the impact and resulting defects.
2. When to Use Mistake Proofing
- Apply mistake proofing whenever there is a process or task prone to errors or high-quality risks.
- Suitable for various fields, including manufacturing and service industries.
- Adaptable to any situation where errors can occur, making it versatile.
- Valuable for improving efficiency, reducing costs, and delivering exceptional results.
- A proactive approach to quality control and process improvement.
3. Benefits of Mistake Proofing
- Significant reduction in defects and errors by implementing foolproof mechanisms.
- Time and resource savings, contributing to improved cost efficiency.
- Simplification of complex processes, resulting in increased productivity.
- Positive impact on employee morale by boosting confidence in task performance.
- Creation of a positive work environment and higher employee engagement.
- Enhanced customer experience with error-free products or services.
4. Principles of Mistake Proofing
- Elimination:
The aim here is to remove error-prone steps by redesigning the product or process. This may entail simplification, part consolidation, or process reconfiguration to eliminate defects upfront.
- Replacement:
Replacement substitutes a more reliable process, often employing automation or robotics to prevent manual assembly errors.
- Facilitation:
This frequently used technique makes a process step easier and less error-prone through methods like visual controls (e.g., color-coding), checklists, and exaggerated asymmetry.
5. Setting and regulatory functions
Setting and regulatory functions are fundamental to error prevention and management within processes.
- Setting functions to inspect process parameters and product attributes for errors using methods like contact or physical examination, motion-step or sequencing checks, fixed-value or counting verifications, and information enhancement.
- Regulatory functions alert workers when errors occur, employing warning functions that utilize sensory signals and control functions that halt the process until errors are corrected or ensure proper conditions before proceeding.
6. Mistake Proofing procedure
To institute a mistake proofing procedure, follow these steps:
- Begin with a comprehensive examination of the process using a flowchart, aiming to identify potential error-prone areas where human errors might arise.
- Delve into the root causes of potential errors by retracing your steps through the process to understand why and where these errors originate.
- Develop error-prevention strategies by considering mistake proofing principles.
- When full error prevention isn’t feasible, work on error detection and mitigation methods. These may include inspection techniques, setting functions, and regulatory controls.
- Choose the most suitable mistake proofing methods or devices for each identified error and rigorously test these solutions before putting them into practice.
- Implement feedback mechanisms for swift error detection. Three inspection methods offer quick feedback which are as follows:
Successive Inspection: Ensure that the next worker in the process checks for errors.
Self-Inspection: Encourage workers to inspect their own work immediately after completion.
Source Inspection: Verify conditions before proceeding with the process, often through automated checks to ensure correct conditions are met.
7. Example
Automated Teller Machines (ATMs):
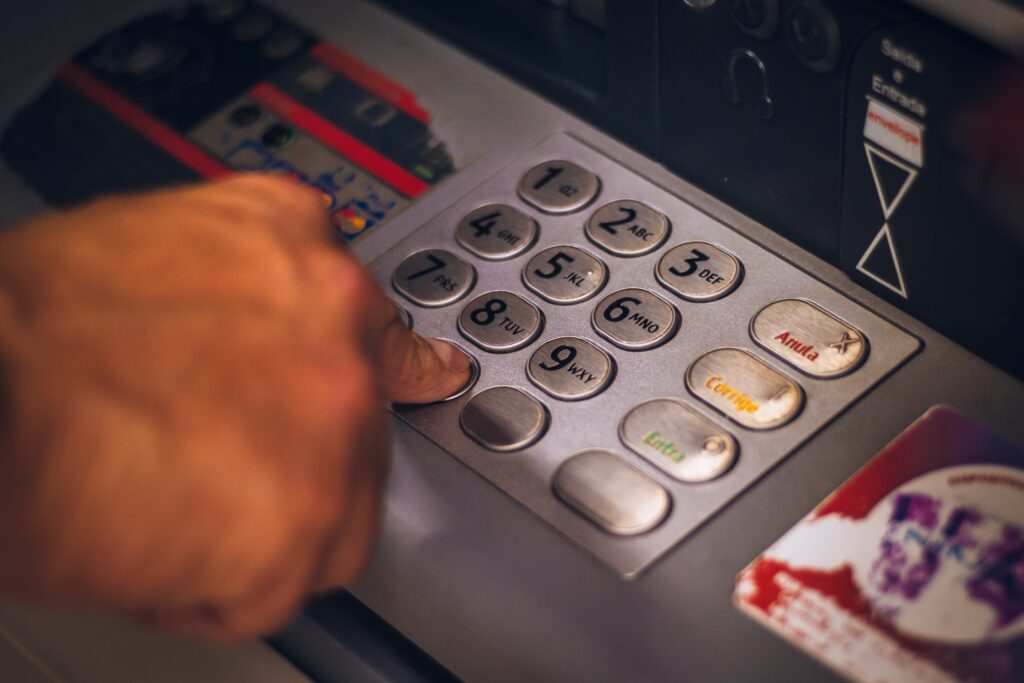
ATMs use confirmatory prompts to prevent customers from making withdrawal mistakes. For instance, when withdrawing a large sum of money, the ATM will often ask the user to confirm the amount before proceeding.
Confirmatory prompts reduce the likelihood of customers inadvertently withdrawing the wrong amount of money, enhancing the user experience and reducing errors.
Pharmacy Prescription Filling:
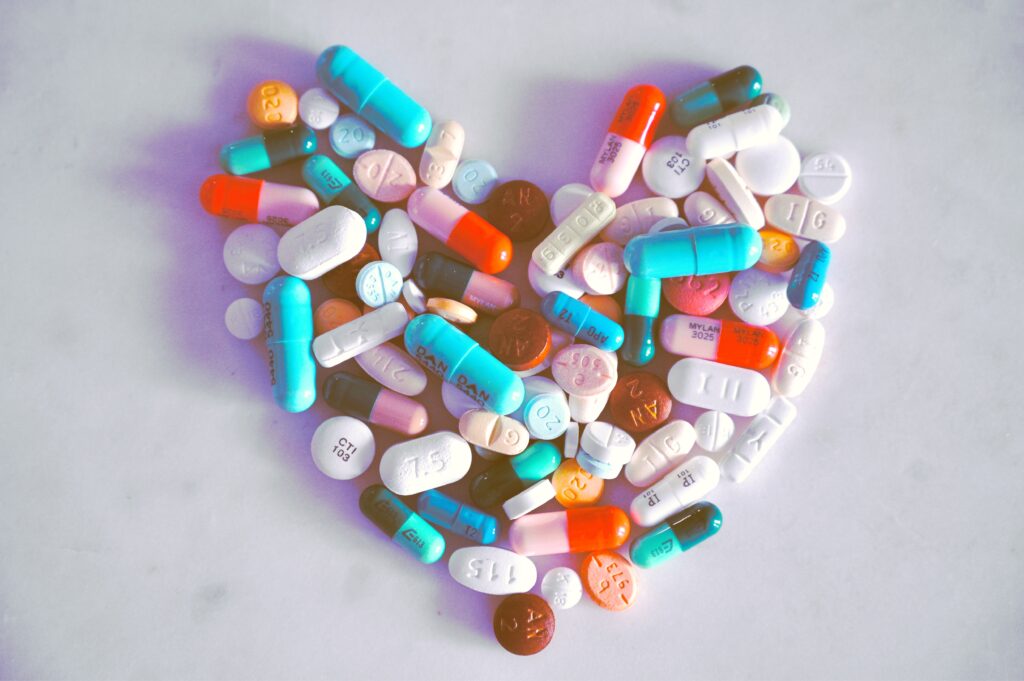
In a pharmacy, the risk of dispensing the wrong medication can have serious consequences. To prevent errors, a barcode scanning system is implemented. Each prescription label and medication container have unique barcodes. Pharmacists and technicians use barcode scanners to match the prescription with the medication, ensuring an exact match before dispensing.
This technique significantly reduces the possibility of medication errors, improving patient safety.
8. Conclusion
In conclusion, mistake proofing, often referred to as poka-yoke or fool-proofing, is a vital approach in various industries to prevent errors and enhance quality. This comprehensive guide has explored its principles, methods, and real-world examples. By implementing mistake-proofing techniques, organizations and individuals can significantly reduce the likelihood of errors, leading to improved efficiency, reduced costs, and increased customer satisfaction.