In a world where organization and efficiency are paramount, the 5S Approach has emerged as a game-changer. Initially developed in Japan, this methodology aims to improve workplace productivity, safety, and morale. In this blog post, we delve into the world of the 5S of Lean, uncovering its powerful benefits and its diverse applications. Whether you are a business owner looking to streamline operations, a manager seeking to enhance employee productivity, or simply someone interested in optimizing your own space, this comprehensive guide will equip you with valuable insights and actionable steps to embrace the transformative power of the 5S Approach. Get ready to revolutionize your surroundings and unlock a new level of efficiency and success.
Understanding the Five S’S (5S) of Lean
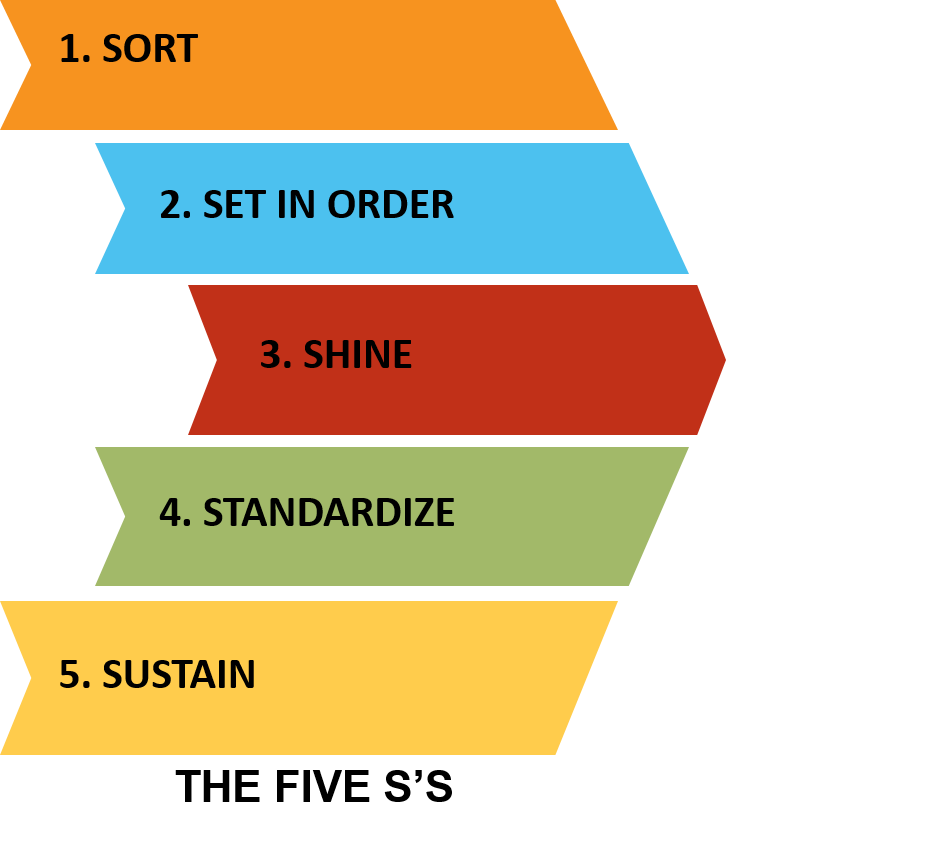
5S is a systematic methodology for organizing and maintaining a clean, effective and productive workspace. It has gained popularity worldwide for improving productivity, safety, and overall workplace efficiency.
The 5S is an acronym for 5 Japanese words that start with the letter “S,” which are as follows:
- Seiri: (Organize)
- Seiton: (Orderliness)
- Seiso: (Cleanliness)
- Seiketsu: (Standardize)
- Shitsuke: (Discipline)
These terms are translated into English as:
- Sort: Remove unnecessary items to create an organized workspace.
- Set in Order: Arrange items logically for easy access.
- Shine: Focus on cleanliness and maintenance.
- Standardize: Implement clear guidelines for consistent organization.
- Sustain: Build a culture of continuous improvement and accountability.
The Five S’S
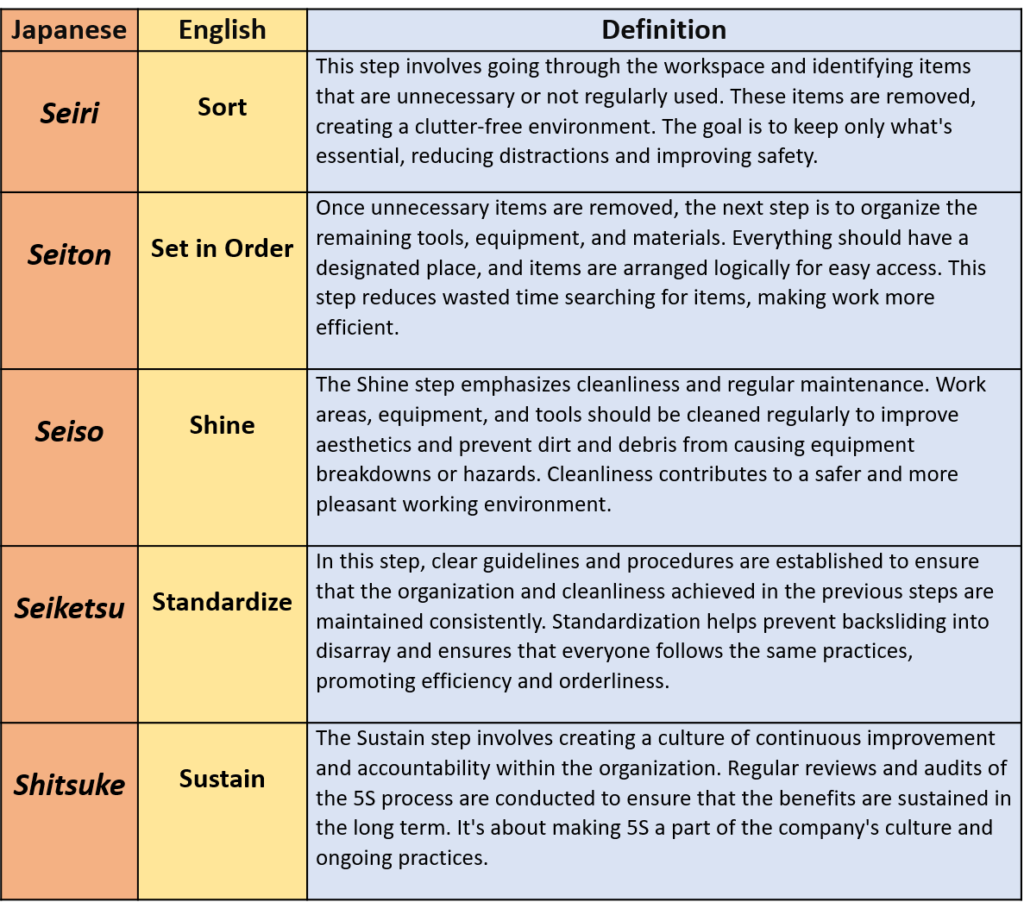
Benefits of 5S Methodology
- Improved efficiency and productivity by optimizing workflow.
- Enhanced workplace safety through a clean and organized environment.
- Elevated employee morale and job satisfaction.
- Reduced waste and increased cost-effectiveness.
- Provides a culture of continuous improvement and innovation.
Application of 5S:
- Manufacturing
- Healthcare
- Software engineering
- Product development
- Public and private sectors
Example
Toyota, a renowned automotive manufacturer, is a prime example of successful 5S implementation. Toyota embraced the 5S principles in their production facilities, resulting in improved efficiency and waste reduction. By organizing their workspaces and implementing standardized processes, Toyota was able to eliminate unnecessary movement and streamline their operations.
Conclusion
In a world where efficiency and organization are paramount, the 5S Approach emerges as a transformative methodology. Originating in Japan, it aims to enhance workplace productivity, safety, and morale through its five fundamental principles: Sort, Set in Order, Shine, Standardize, and Sustain. This systematic approach finds application in various sectors, including manufacturing, healthcare, and office spaces. By embracing the 5S Approach, organizations can unlock benefits such as improved efficiency, safety, and employee satisfaction while fostering a culture of continuous improvement. It’s a powerful tool for anyone seeking to revolutionize their surroundings and achieve a new level of success through organization and efficiency.