In any organization, it is crucial to clearly understand its processes and how they contribute to the business’s overall success. This is where the SIPOC+CM diagram comes into play. SIPOC, which stands for Suppliers, Inputs, Process, Outputs, and Customers, is a powerful tool for mapping the high-level process flow. Combined with the CM (constraints, measures) diagram, it provides a comprehensive view of the entire process, highlighting key inputs, outputs, and critical quality parameters. In this blog post, we will delve into the benefits of using the SIPOC+CM diagram and walk you through the step-by-step procedure of creating one. Whether you are a process improvement professional or simply looking to enhance the efficiency of your organization, this guide will equip you with the knowledge and tools to unravel the benefits of the SIPOC+CM diagram and implement it effectively.
Introduction to the SIPOC+CM Diagram
In Six Sigma process improvement, the SIPOC+CM diagram is a powerful tool that helps organizations understand their processes and identify areas for improvement. It is a data collection tool that provides a visual representation of the process flow by mapping out the Suppliers, Inputs, Processes, Outputs, and Customers (SIPOC) involved in the process. The “+C” represents the constraints within the system, and the “+M” indicates the measures that will be utilized.

Benefits of SIPOC+CM Diagram
- Enhances process transparency
- Boosts communication across roles
- Pinpoints inefficiencies for improvement
- Facilitates risk identification and mitigation
- Elevates productivity and customer contentment
- Underpins informed decision-making
- Encourages ongoing process optimization
When to use SIPOC+CM Diagram
- Gather essential information before constructing a flowchart.
- Understand the fundamental components of the process during the investigation.
- Record collective knowledge in an easily digestible format.
- Communicate process details concisely to others.
SIPOC+CM Diagram Procedure
1. Sketch a SIPOC+CM diagram on a broadsheet, marking seven sections for each SIPOC+CM element.
2. Clearly define the focus process and its scope, setting clear start and finish points to ensure a collective understanding of the analysis boundaries.
3. In the designated sections for SIPOC+CM, capture the corresponding information:
- Suppliers: Identify the sources (people or systems, internal or external) that supply inputs to the process.
- Inputs: Detail the specific materials or information the process requires.
- Process: Outline the five to seven main steps at a high level, similar to an overview from “35,000 feet”.
- Outputs: List the end products, services, or technologies the process yields.
- Customers: Note the primary recipients or users of the process outputs.
- +C: List any limitations or restrictions the process faces.
- +M: List the measures for assessing the process.
4. Validate the diagram’s thoroughness with stakeholders, project sponsors, and other parties with a vested interest.
Example of SIPOC+CM Diagram
The following figure shows a high level of SIPOC+CM example:
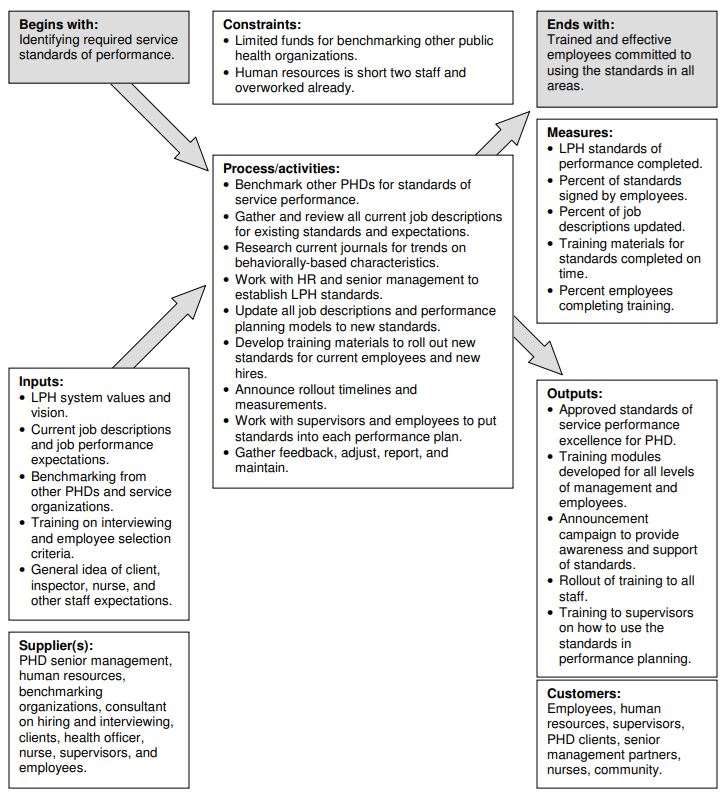
Example # 2: E-Commerce Customer Service Improvement
As a project manager, you’re tasked with enhancing the customer service process of an e-commerce company, presenting a perfect scenario to apply the SIPOC+CM diagram.
SIPOC Elements Identification
- Suppliers: Include vendors, software systems, and customer service representatives
- Inputs: Comprise customer inquiries, product information, and order details
- Process: Encompasses stages such as ticket routing, response drafting, and issue resolution
- Outputs: Involve resolved customer queries and satisfaction ratings
- Customers: The end-users or customers seeking support
- CM Aspect Integration: Change Analysis
With the process mapped, it is considered to implement an automated ticketing system, analyzing its impact on each SIPOC element.
Conclusion
In conclusion, the SIPOC+CM diagram is invaluable in Six Sigma process improvement, offering a clear, comprehensive view of organizational processes. Its ability to enhance transparency, improve communication, and identify inefficiencies makes it instrumental in driving meaningful improvements. By facilitating targeted changes and strategic planning, the SIPOC+CM diagram optimizes processes and significantly boosts customer satisfaction and overall business performance.