In today’s fast-paced and competitive business world, organizations must constantly seek ways to improve their processes, products, and services to stay ahead. This is where the PDCA (Plan-Do-Check-Act) cycle comes into play. The PDCA cycle, or the Deming cycle, is a powerful and proven method for achieving continuous improvement. It provides a systematic approach to identifying areas for improvement, implementing changes, and evaluating the results. In this comprehensive guide, we will explore the various steps of the PDCA cycle, understand its significance, and discover how it can drive positive change and help organizations thrive in an ever-evolving landscape.
HISTORY OF PDCA CYCLE
Walter Shewhart, recognized as the father of statistical quality control, initially introduced the PDCA cycle. In his book, he applied scientific methods to quality control in manufacturing. W. Edwards Deming later expanded on Shewhart’s ideas, applying them to quality control and improving processes in general.
Deming introduced the method, initially named the Shewhart cycle, to engineers in Japan. In Japan, they combined this cycle with Kaizen, a concept of continuous improvement developed by Kaoru Ishikawa, and integrated it with the Toyota production system and lean manufacturing principles. This integration led to the evolution of what is today known as the Plan-Do-Check-Act (PDCA) cycle.
PDCA is also known as the “Plan-do-study-act (PDSA) cycle, Deming cycle, Shewhart cycle”
WHAT IS PDCA CYCLE?
The PDCA (Plan-Do-Check-Act) cycle is a dynamic, continuous problem-solving and process improvement approach. In this ongoing loop, teams develop plans, implement them, assess the outcomes, and then utilize the insights gained for further enhancements.
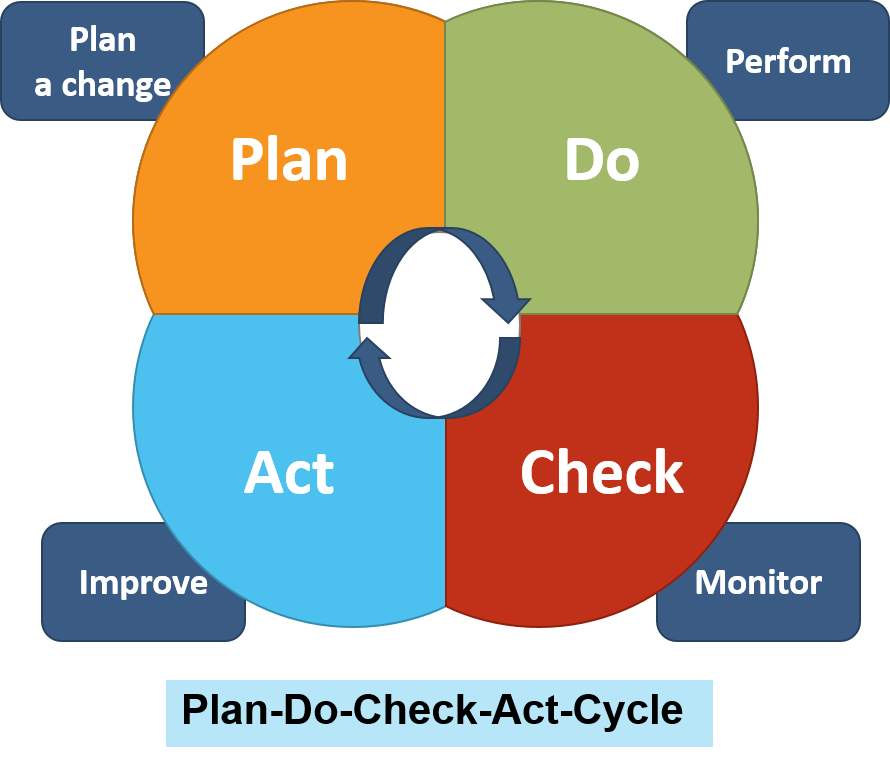
This cycle is particularly effective in addressing business challenges due to its flexibility and emphasis on step-by-step, iterative progress. The PDCA cycle consists of four distinct steps: Plan, Do, Check, Act and resembles a perpetual circle, designed for continuous repetition. This repetition ensures sustained improvement, reflecting the cycle’s core principle of fostering constant process development and refinements.
PLAN, DO, CHECK, ACT (PDCA) PROEDURE
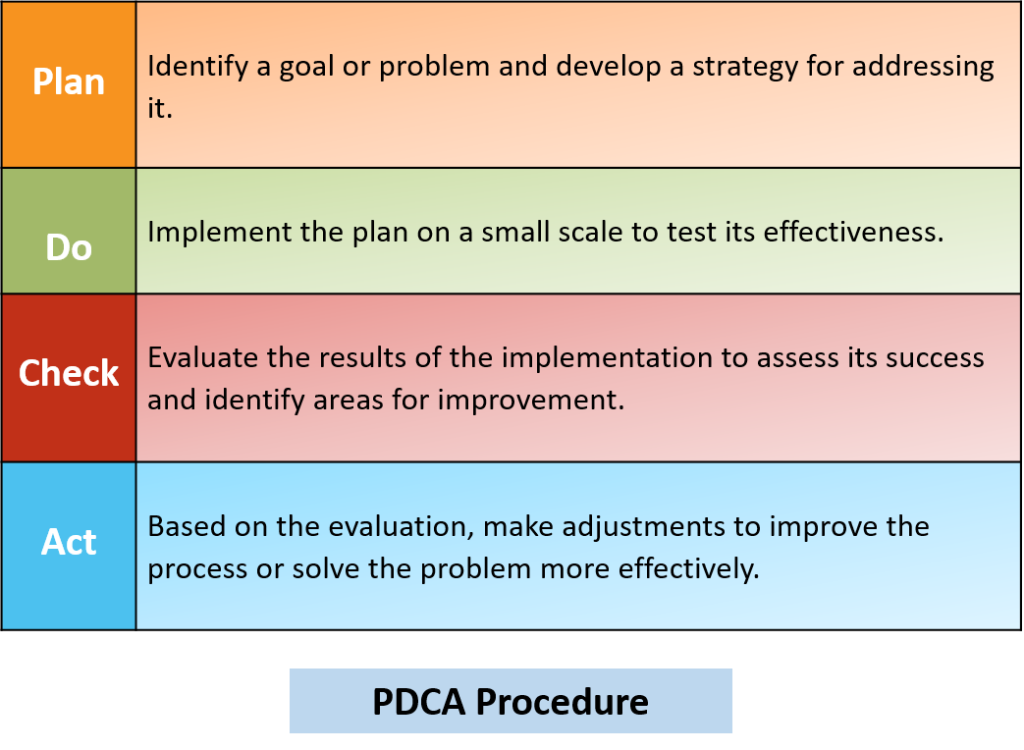
Plan Phase
In the Plan Phase, the focus is on identifying the core problems or setting specific goals, followed by developing a strategic action plan to address them. This involves setting clear, measurable objectives and defining the project’s scope, ensuring everyone understands the targets and limits. Data analysis and thorough research play a crucial role in this phase, providing a well-informed basis for the strategy and ensuring the plan is grounded in reality.
Do Phase
The Do Phase involves the actual implementation of the planned activities. This is where the strategy is put into action. Key aspects of this phase include effective team coordination to ensure that all members are aligned and working towards the common objectives and progress monitoring to track the implementation’s progress. Additionally, data is collected during this phase, which will be critical for subsequent evaluation and assessment.
Check Phase
In the Check Phase, the results of the implemented plan are evaluated against the expected outcomes. This involves a detailed analysis of the data collected during the Do Phase to assess the plan’s effectiveness. Here, the focus is identifying deviations from the expected results and pinpointing improvement areas. This phase is essential for understanding the action’s impact and learning from the outcomes.
Act Phase
Finally, the Act Phase is about taking corrective actions based on the insights gained from the Check Phase. This includes making necessary adjustments and refinements to the plan to achieve enhanced outcomes. It is a phase where the lessons learned are applied to improve the process or approach continuously. This phase closes the cycle but also sets the stage for the next repetition of the PDCA cycle, ensuring ongoing process improvement.
BENEFITS OF PDCA CYCLE
- Encourages creative problem-solving and continuous improvement.
- Identifies and eliminates inefficiencies in processes.
- Proactively manages and enhances quality standards.
- Facilitates informed decisions based on empirical data.
- Optimizes processes and resource utilization.
- Encourages learning and adaptation through regular feedback.
- Supports long-term success through ongoing refinement and adaptation.
WHEN TO USE PDCA CYCLE
The PDCA cycle is best used for:
- Launching initiatives to enhance processes or systems.
- Creating or improving designs of processes, products, or services.
- Establishing or optimizing routine operations.
- Collecting and analyzing data to identify and address root causes.
- Systematically applying changes for effective implementation.
- Ongoing enhancement and refinement in various areas.
- Quickly testing and adapting solutions for immediate results.
EXAMPLE OF PDCA
General Electric (GE)
General Electric, a multinational conglomerate, has extensively employed the PDCA cycle for various process improvements, particularly in its healthcare division. GE implemented the PDCA cycle to enhance the efficiency of their medical equipment manufacturing processes.
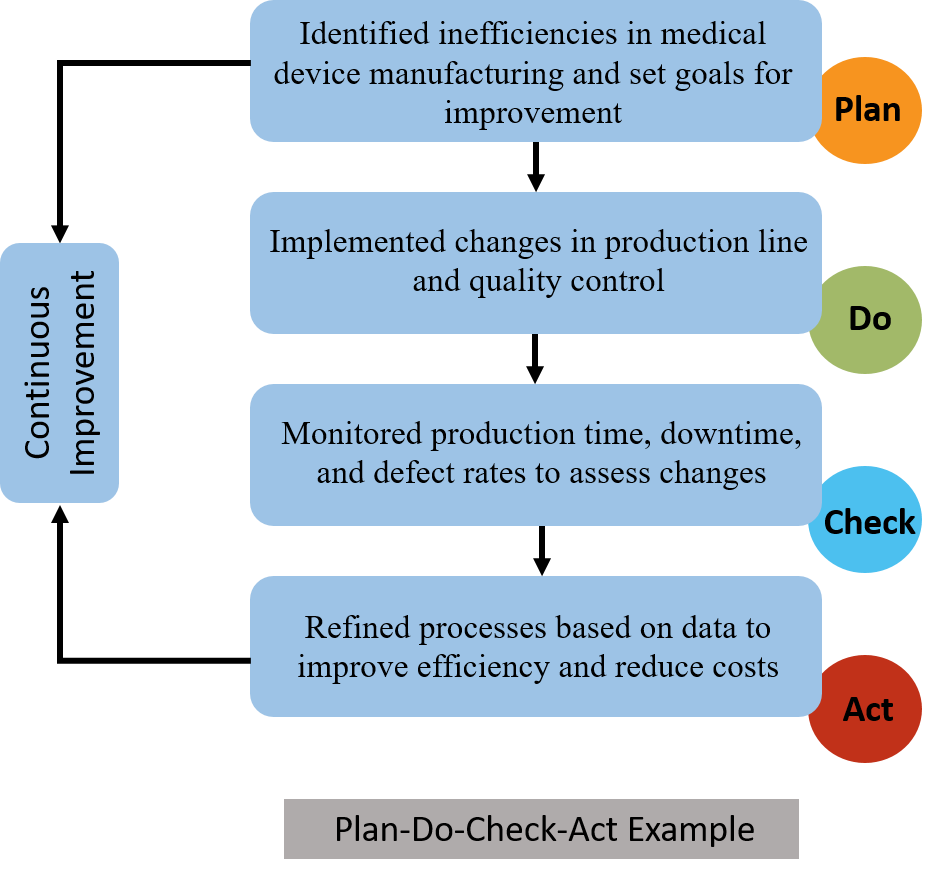
Conclusion
In summary, the PDCA (Plan-Do-Check-Act) cycle, originating from the works of Walter Shewhart and W. Edwards Deming, is a fundamental approach for continuous improvement in business and personal endeavors. It blends planning, action, evaluation, and iterative refinement, making it versatile for various applications. The cycle’s adaptability and focus on progressive improvement offer significant benefits, including enhanced efficiency, quality control, teamwork, and customer satisfaction. As a methodology, PDCA is essential for achieving sustainable growth and long-term success, applicable in various sectors and for diverse objectives.